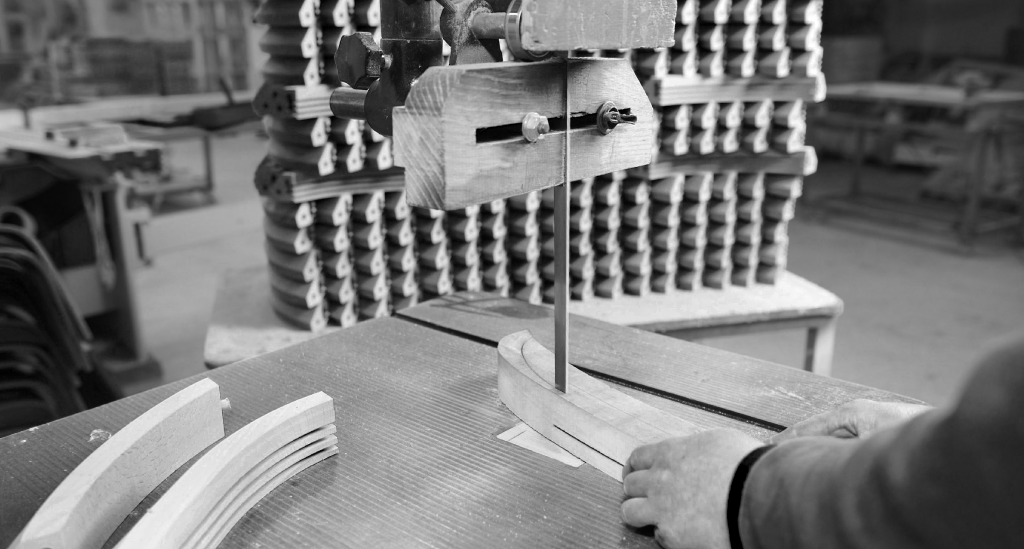
Let’s Start with Materials!
Whilst it is a very common subject now, buzzwords abound, being fully circular in the fields of design and manufacturing is no easy feat.
The pressure to become more sustainable can become a burden that many manufacturers find difficult to address in between the day to day of production and distribution, especially if this is a global company.
Yes, we are ever aware of the state of the environment. Yes, we feel guilt in our personal and work lives reference to behaving more thoughtful and more well intentioned towards mother earth, but where can we glean inspiration to become leaders in sustainability.
The fact that some companies are way ahead is motivation but can add to the worry that one is not achieving enough, quick enough when others seem so ahead. I believe, simplifying is key; when it comes to furniture manufacturing how can we break it down, so that it is less daunting and companies are encouraged to take one small step at a time towards the bigger final goal.
In furniture, in simple terms, the circular economy covers:
Materials
Production
Packaging
Distribution
End of Life
Is it possible to tick boxes under each heading? It would seem difficult, or near impossible in a global economy, but while we can tackle more simpler tasks, with the more unsolvable problems we can maybe only seek alternative solutions There definitely are areas we can make changes in, and other areas can be optimised.

In manufacturing the first port of call would be the materials that are being used. Even before we examine the production methods and chemicals that are used, we can make changes in this area. Wood, foam, dacron, other fillings, webbing, springs, fabrics and threads…
In furniture manufacturing we really need to look over these elements, seek alternatives and start using the more sustainable alternatives. The concern has always been that the costs will be more, and this will affect a manufacturer’s competitive edge in the global market place, but this is a ‘chicken and egg’ situation, the more the manufacturer’s make changes and use more sustainable materials, the more the prices will lessen. As demand grows variety will also increase, and consequently prices will become more accessible for mass manufacturing.
Re-educating ourselves is the first stop, and then truly thinking outside the box is the next stop. Wood that is used in furniture manufacturing, of course, as an absolute minimum, should be FSC certified, however if we are able to look at the situation from a wider angle, could we not start using reclaimed wood and plywood more in manufacturing?
We can continue to believe the myth, for example, that there isn’t much choice out there in the area of fabrics made from recycled components, to then find out that the choice is growing at a rapid speed now, with companies even fashioning high quality lush velvet that is made with recycled ‘stuff’.
Similarly it is possible to use reclaimed foam, dacron made from recycled fabrics, and the list gets longer…
The starting point is the intent to make change towards protecting our environment, and then setting SMART goals to lessen harm to the environment. My suggestion is that a manufacturer aims to research and change its materials to become fully sustainable alternatives within a period of 24 months. Small steps need not be daunting, and each achievement will be the right tonic to get more and more motivated to becoming an environmentally responsible manufacturer.
Jade Ilke
www.designingfutures.today
in collaboration with Parla